[ad_1]
The Ford GT40 is a sports car with a history that was designed in just 126 examples in the 1960s and is well known to car enthusiasts and enthusiasts alike – the rivalry between Henry Ford II and Enzo Ferrari inspired more than just a movie. In any case, the vehicle is at the center of the present: in the United States, a collector car enthusiast Chris Ashton used 3D technologies to modify and customize his Ford GT40, especially thanks to Artec Space 3D scanners Spider and Artec Eva. The collector was thus able to reproduce complex shapes very quickly, as closely as possible, and hopes to be back on the road as soon as possible.
3D scanners are often used to digitize period objects and parts, making it possible to obtain a digital copy. This can then be modified, personalized and then 3D printed to have a physical model. This is a particularly interesting point for spare parts design in the automotive industry: most spare parts for classic cars are no longer produced, thus complicating maintenance and repair tasks and increasing costs significantly. However, thanks to a 3D scanner, the user can easily digitize the original part and, thanks to additive manufacturing, reconstruct a digital and then a physical model.
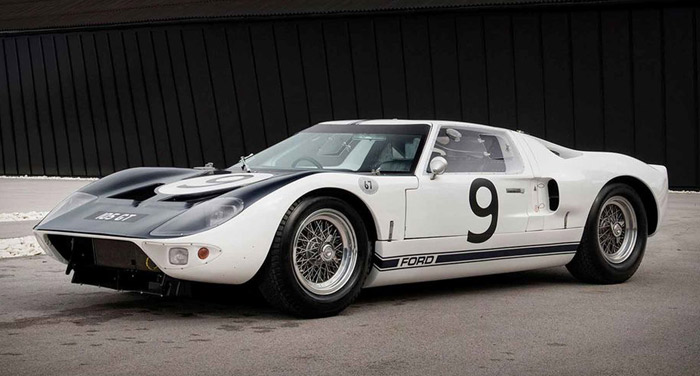
Photo credit: Ford
Artec solutions for Ford GT40 customization
Chris Ashton is passionate about cars and has managed to combine that passion with his professional activities: Ruffian Cars is a Californian company that manufactures and modifies sports cars. It has been using additive manufacturing to remanufacture spare parts for several years, but the process required many iterations before getting a model as close as possible to the original part. That’s why Artec Space Spider and Artec Eva scanners, especially car spacers.

Chris Ashton explains:Previously, I had to shape the spacers directly on the car out of foam or clay and take the whole car to a shop to have them make the molds (or make them myself, but that’s complicated and a lot of chemicals). And I had to do it twice because in the real world it is impossible to create a symmetrical version of a part. The main advantage here is that the fender flares are digitally generated on a scaled scan of the real car. So we were sure they had the right size and that the left and right edges would be perfectly symmetrical.”
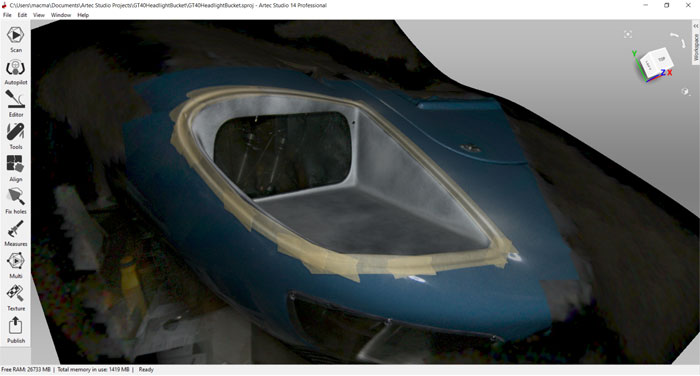
Angles and interior curves of the headlight housing 3D scanned (photo credit: Artec 3D)
Chris says the Artec Eva scanner allows it to scan the entire vehicle; The Space Spider was used to scan smaller parts and zoom in on items to be integrated. It is an ideal scanner for capturing the reality of small objects, especially suitable for applications that require fine detail and precision. The company can then import all the vehicle data in 3D software, see the real-time engagement of parts, etc. Chris continues:Since the scans are full-size to the computer, I can model my new pieces around them and print them without worrying about scale. This is a huge improvement over what I’ve done before. : take the measurements manually and build my pieces from them, hoping they are correct.” The 3D printing process is therefore easier and fairer.
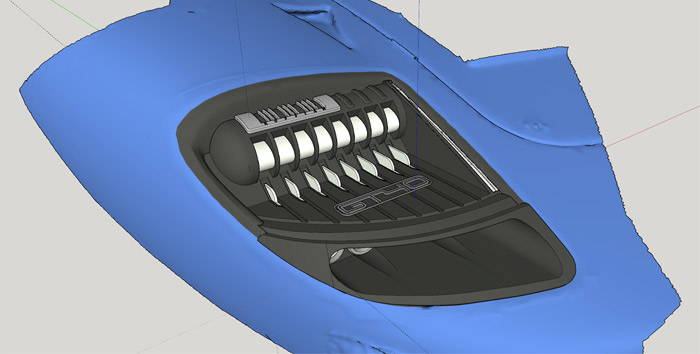
Assembled lighthouse model (photo credit: Artec 3D)
Chris Ashton’s work doesn’t stop with the reproduction of Ford GT40 flares: his customization work extends to the buckles of the seat belts, but also to the fenders and side skirts. In November, Ford will present its GT40 at SEMA 2021, a trade show where automakers showcase their products. You can find more information about Artec 3D 3D scanners HERE.
*Cover photo: Artec 3D
What do you think about the use of scanning solutions to repair classic cars? Feel free to share your views in the comments of the article or with members. 3Dnatives forum. You can find all our videos on our channel. YouTube or follow us Facebook Where excitement !
[ad_2]
Source link